How Packaging Equipment Repair Services Contribute to Workplace Safety
How Packaging Equipment Repair Services Contribute to Workplace Safety
Blog Article
Recognize the Benefits of Utilizing Professional Product Packaging Equipment Repair Provider
Using expert packaging devices repair services presents a number of crucial benefits for businesses. Boosted tools long life and improved operational efficiency are notable advantages. Experienced service technicians can promptly attend to concerns, stopping small problems from intensifying into significant downtime. Furthermore, normal maintenance supports conformity with market criteria, making sure safety and security and protecting brand track record. Understanding just how these elements add to overall performance is important for any type of company aiming to enhance its operations. What ramifications does this have for future development?

Boosted Equipment Long Life
Correct maintenance via expert packaging equipment repair work services substantially adds to boosted equipment long life. By addressing wear and tear without delay, these solutions aid protect against minor issues from escalating into major breakdowns. Competent technicians possess the requisite knowledge and experience to determine possible issues that may not appear to untrained workers. Normal inspections and timely repairs ensure that machinery operates within excellent parameters, reducing the threat of devastating failures.Moreover, professional repair solutions commonly make use of high-grade substitute parts, which can considerably prolong the lifespan of equipment. This proactive strategy not just reduces downtime however additionally fosters a consistent production circulation. Services that purchase specialist upkeep are most likely to see a much more trusted efficiency from their product packaging devices, inevitably bring about decreased expenses connected with frequent substitutes. Essentially, the durability of packaging equipment is directly influenced by the commitment to routine and expert repair service solutions.
Improved Operational Effectiveness
Investing in specialist packaging tools repair services straight enhances functional efficiency (Packaging Equipment Repair Services). Professional service technicians possess specialized understanding and skills, allowing them to identify and solve concerns promptly, lessening downtime. By ensuring that devices runs at peak performance, organizations can maintain constant production routines, consequently meeting client demands a lot more effectively.Furthermore, routine upkeep and timely repair work prevent minor problems from escalating right into significant failures, which might disrupt operations and cause costly delays. With properly repaired equipment, employees can concentrate on their core jobs instead of repairing malfunctioning machines.The integrity of well-maintained packaging equipment adds to smoother operations, enabling companies to enhance their manufacturing procedures. Ultimately, this positive strategy not just improves procedures however additionally fosters a more effective workplace, enabling companies to adapt to transforming market needs with greater dexterity. Boosted functional performance becomes a keystone for sustained development and competition in the product packaging market
Cost Financial Savings on Repair Works
Applying professional product packaging tools repair services can cause considerable price financial savings for businesses. By addressing repair service requires quickly and successfully, companies can stay clear of the high expenses connected with prolonged devices downtime. Delays out of commission machinery can cause shed manufacturing, which directly influences profits. Additionally, specialist fixing services typically supply bulk or regular upkeep, lowering the probability of significant failures in the future.In enhancement, using specialized solutions can extend the life-span of tools, minimizing the need for expensive substitutes. Businesses can also gain from foreseeable repair service costs, enabling much better budgeting and monetary planning. Furthermore, outsourcing repairs can release up internal sources, enabling team to concentrate on core procedures rather than fixing devices issues. Generally, professional product packaging devices repair work solutions use a calculated strategy to taking care of fixing expenditures, ultimately improving a company's profits while guaranteeing operational connection.
Accessibility to Expert Knowledge and Abilities
While organizations may have skilled staff, counting on expert packaging equipment fixing solutions provides accessibility to a wider variety of professional expertise and specialized skills. These professionals are often learnt the current innovations and sector criteria, which enables them to address complicated concerns that in-house teams could not be geared up to handle. Their experience spans different tools kinds and brands, permitting them to swiftly identify issues and apply efficient solutions.Moreover, professional fixing service technicians remain upgraded on advancements and finest methods, ensuring that repair services are performed effectively and efficiently. This degree of experience can bring about enhanced devices long life and efficiency, ultimately profiting the business's lower line. By using these specialized services, services can use a riches of understanding that improves their functional abilities without the need for comprehensive inner training or financial investment in extra resources. This calculated method assists keep the honesty of product packaging procedures while maximizing resource allocation.
Reduction of Downtime
Minimizing downtime is essential for preserving operational effectiveness in product packaging centers. Quick feedback times, coupled with expert troubleshooting abilities, permit service technicians to address concerns immediately. Furthermore, reliable fixing procedures assure that tools is recovered to come to a head efficiency with minimal disturbance.
Quick Action Time
A swift feedback time is essential for services counting on packaging tools, as even minor delays can cause considerable operational disturbances. When equipment breakdowns, punctual interest from specialist repair solutions can substantially minimize downtime, permitting manufacturing routines to resume swiftly. Quick reaction times not just minimize the impact on total efficiency yet likewise aid keep customer complete satisfaction by meeting distribution timelines. Expert repair solutions frequently focus on urgent demands, making certain that professionals are readily available to deal with issues as they arise. This level of responsiveness is vital in affordable industries where effectiveness is vital. Ultimately, businesses take advantage of a reputable partnership with fixing solutions that recognize the necessity of their functional needs, cultivating a positive approach to devices maintenance and administration.
Professional Troubleshooting Skills
Specialist troubleshooting skills are important for reducing downtime in product packaging operations. Experienced professionals have the ability to promptly identify the origin of equipment breakdowns, which is vital in maintaining operational efficiency. They utilize their comprehensive expertise and experience to identify problems properly, ensuring that potential problems are dealt with prior to they escalate. This aggressive approach reduces the threat of prolonged interruptions and boosts productivity. Furthermore, specialist troubleshooters can carry out targeted solutions that protect against repeating issues, resulting in a much more trustworthy product packaging process. Their expertise not only conserves time yet also reduces the financial impact of unforeseen break downs. In a market where time is money, having access to efficient troubleshooting abilities is a very useful property for any kind of packaging procedure.
Reliable Repair Work Processes
Efficient repair work processes play an important role in decreasing downtime for product packaging equipment. Speedy medical diagnosis and reliable implementation are crucial parts that make it possible for specialists to determine More hints issues swiftly and carry out remedies without unnecessary hold-ups. Expert repair service solutions typically utilize sophisticated tools and technologies, enabling even more accurate repair services and decreasing the likelihood of persisting problems. Organized workflows and standardized treatments improve the repair service procedure, making certain that repair services are finished consistently and efficiently. This effectiveness not just recovers devices capability yet additionally boosts general functional efficiency. By purchasing expert repair solutions, organizations can considerably lower the time equipment remains still, eventually leading to boosted profitability and operational dependability in their product packaging procedures.
Compliance With Industry Requirements
Compliance with industry criteria is necessary for making certain the stability and safety of product packaging devices. Following regulative requirements and tools safety requirements not only protects employees but also improves functional efficiency. Carrying out sector ideal techniques is vital for keeping conformity and cultivating a society of safety and security and top quality within organizations.
Governing Compliance Guarantee
Making certain regulative compliance in packaging devices repair is necessary for keeping industry requirements and securing product stability. Professional fixing services are well-versed in the specific policies controling packaging processes, ensuring that all repair work meet the necessary lawful requirements. This experience reduces the risk of non-compliance, which can lead to costly penalties and disruptions in manufacturing. Furthermore, adherence to governing requirements helps in preserving brand name online reputation and consumer count on. By making use of specialized fixing solutions, business can enhance their procedures while ensuring that their tools operates within the structure of market guidelines. This aggressive approach not only improves operational efficiency but likewise reinforces dedication to top quality and safety in the packaging industry.
Devices Safety And Security Specifications
While lots of business focus on performance in their product packaging operations, adherence to tools security requirements is vital for preventing mishaps and ensuring a safe workplace. Conformity with these requirements aids mitigate threats connected with equipment usage, shielding both properties and employees. Expert product packaging devices repair services play an essential function in preserving safety by making certain that equipments are consistently checked, serviced, and upgraded according to industry guidelines. This aggressive method not just boosts operational dependability but also cultivates a culture of safety and security within the workplace. By purchasing professional fixing solutions, business can attain compliance with security criteria, lower liability dangers, and eventually advertise a much safer, more productive setting for their labor force.
Sector Best Practices
Adhering to industry finest methods is important for product packaging companies aiming to keep operational excellence and regulative compliance. Compliance with industry standards not just enhances item top quality however likewise decreases risks connected with tools breakdowns and safety and security hazards. Regular training and certification for service technicians guarantee that they are well-versed in the newest repair service strategies and security protocols. Additionally, regular upkeep timetables assist in determining potential problems before they rise, thereby extending equipment life. Utilizing standard treatments and documents methods assists in consistency and accountability. By welcoming these ideal practices, packaging companies can enhance efficiency, reduce downtime, and promote a culture of security and reliability, ultimately leading to increased consumer fulfillment and loyalty.
Increased Safety And Security in the Office
As companies prioritize the health and wellness of their staff members, the duty of expert packaging equipment fixing services becomes progressively important in enhancing office security. Well-maintained tools significantly reduces the threat of mishaps, injuries, and devices malfunctions. Specialist technicians possess the experience to determine prospective dangers and implement essential repair services quickly, ensuring that machinery operates within risk-free parameters.Regular assessments and maintenance by certified professionals additionally mitigate the chances of unexpected break downs, which can bring about harmful scenarios on the production flooring. By utilizing these solutions, companies promote a culture of safety that focuses on staff member health. Furthermore, compliant and upgraded devices sustains adherence to industry laws, lessening lawful risks connected with workplace safety and security violations - Packaging Equipment Repair Services.Ultimately, purchasing expert packaging devices repair work solutions not just safeguards workers but additionally boosts functional efficiency, causing an extra productive workplace atmosphere
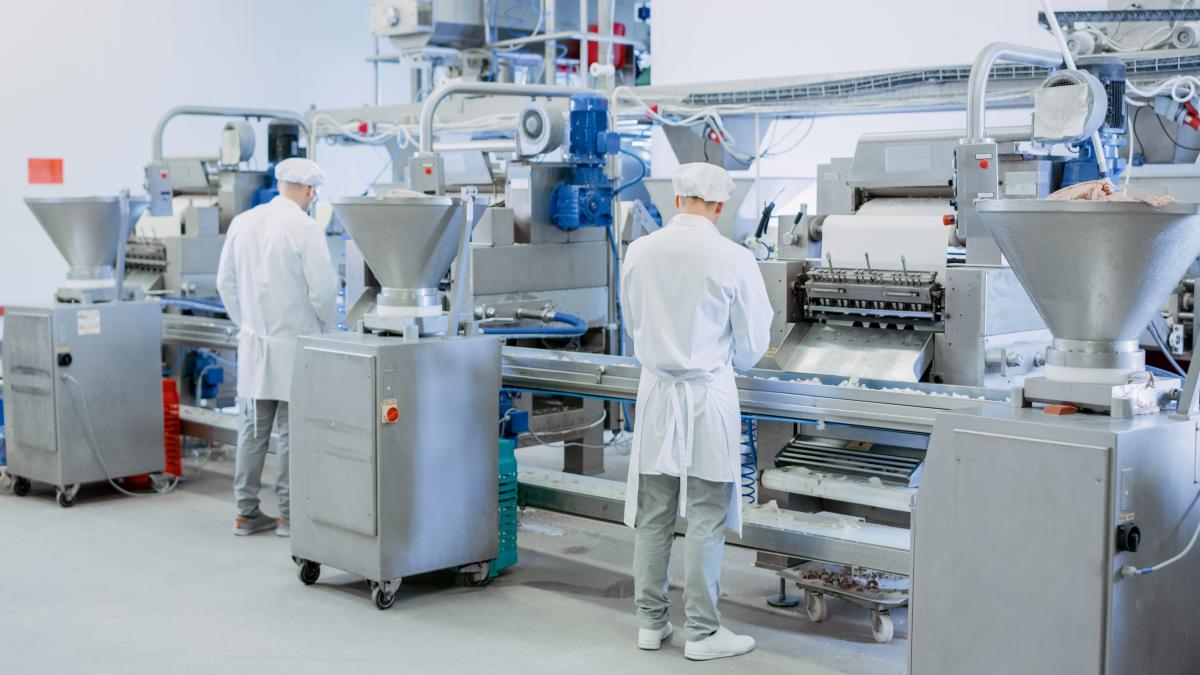
Regularly Asked Inquiries
How Do I Pick the Right Product Packaging Devices Repair Service Solution?
Selecting the best packaging equipment fixing service entails assessing expertise, client testimonials, action times, and guarantee alternatives. Furthermore, reviewing the service's knowledge with certain equipment and accessibility of parts can substantially affect the decision-making procedure.
What Kinds Of Product Packaging Equipment Can Be Fixed Properly?
Numerous types of packaging devices can be fixed expertly, consisting of loading devices, labeling devices, sealing equipments, and palletizers. Each kind calls for specialized understanding to guarantee efficient fixings and maximum functional performance in packaging procedures.
How Commonly Should I Set Up Maintenance for My Product Packaging Tools?
Arranging maintenance for product packaging tools need to take place every 3 to six months, relying on use intensity and producer recommendations. Normal maintenance warranties peak performance, extends equipment life-span, and decreases unexpected malfunctions that can interfere with procedures.
Exist Warranties on Fixes Provided by These Providers?
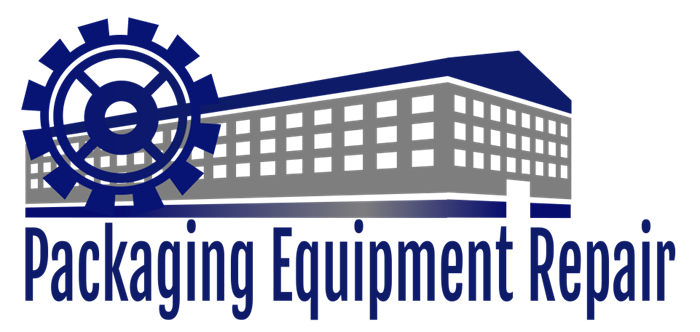
What Should I Do if My Tools Damages Down Unexpectedly?
When equipment breaks down unexpectedly, it is advisable to assess the issue, guarantee safety, seek advice from the manual for repairing tips, and get in you can find out more touch with a qualified service technician for expert support to lessen downtime and warranty effective repair work. Proper maintenance via specialist packaging tools repair service solutions substantially adds to improved devices long life. Timely repair services and routine evaluations assure that equipment runs within ideal criteria, reducing the risk of devastating failures.Moreover, specialist repair service services usually utilize top quality replacement parts, which can significantly prolong the life-span of equipment. With skillfully repaired devices, workers can focus on their core jobs rather than troubleshooting malfunctioning machines.The dependability of properly maintained packaging devices adds to smoother procedures, allowing companies to maximize their manufacturing procedures. Their experience extends numerous devices kinds and brands, enabling them to swiftly detect issues and execute efficient solutions.Moreover, specialist repair service specialists stay upgraded on advancements and ideal practices, ensuring that repair services are executed effectively and successfully. Properly maintained devices substantially reduces the danger of crashes, injuries, and equipment breakdowns.
Report this page